Renovation Quality Control – The Foundation of Excellence
Table of Contents
The Renovation Quality Control Standards process aims to eliminate common pitfalls by implementing rigorous inspections and quality of work at every stage of the project. From checking for structural integrity to analysing construction materials specifications, this process ensures that your renovation meets not only style standards but also safety standards regulations.
What is Renovation Quality Control
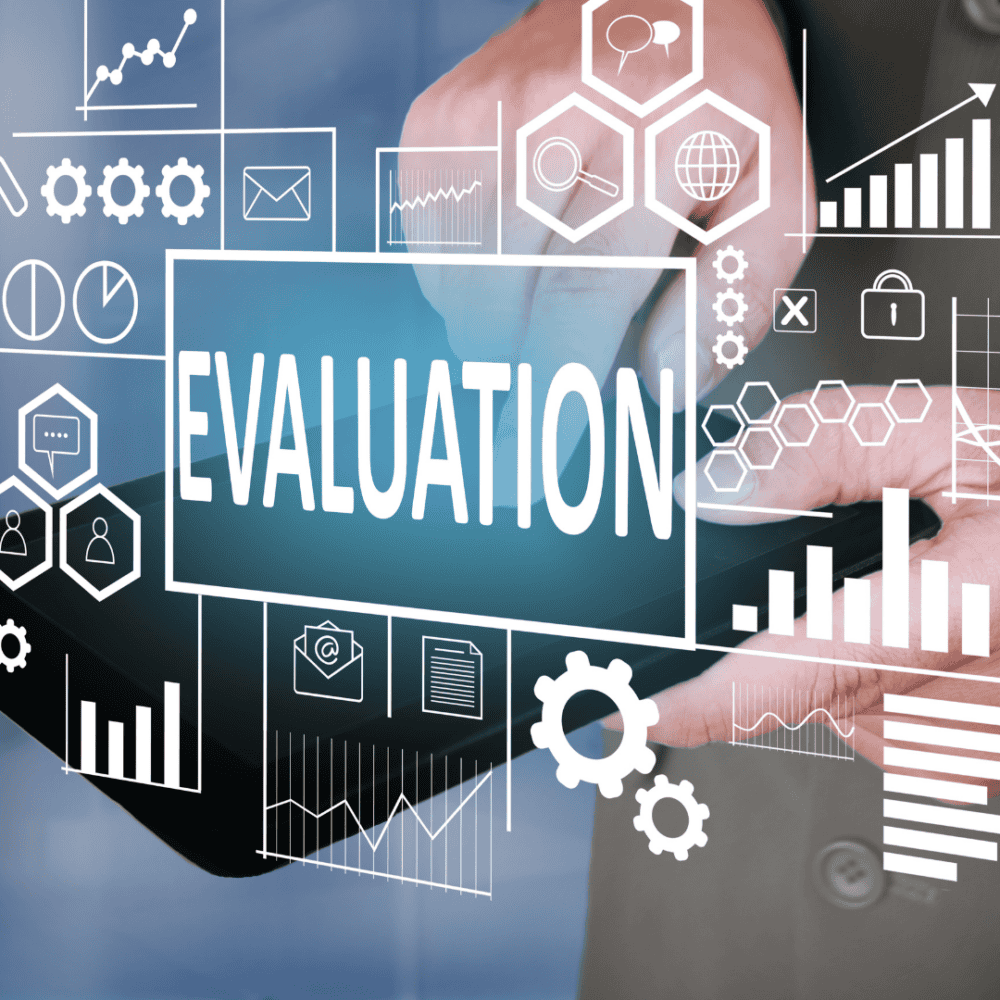
Renovation Quality Control is a vital aspect of any construction project, ensuring that the final outcome meets or exceeds industry standards. It involves a comprehensive evaluation and monitoring building process aimed at identifying and rectifying potential flaws or deficiencies throughout the renovation journey. From the initial planning phase to the execution and completion of the project, quality control plays an essential role in maintaining consistency, efficiency, client expectations and also customer satisfaction.
One key element of renovation quality control is conducting a regular inspection process at various stages of the renovation process by the QA team. These inspections involve thorough checks for the vital step of structural integrity, adherence to safety codes, compliance with design specifications and overall workmanship. By quality control managers identifying any number of defective issues early on, the construction management can take corrective measures promptly to prevent costly mistakes or rework down the line.
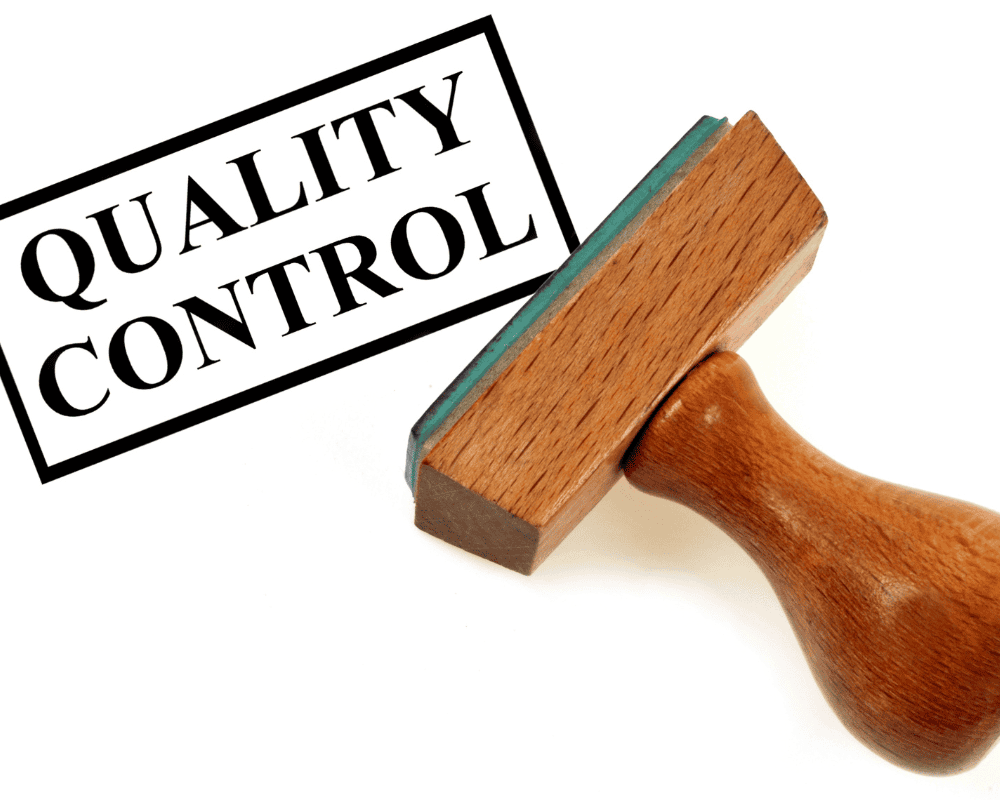
Another critical component of quality control procedures in renovations is assessing suppliers’ materials and selecting reputable vendors. Ensuring that only high-quality materials are used not only enhances the durability and longevity of the renovated space but also contributes to its style appeal. Additionally, by partnering with trusted suppliers who adhere to industry standards for production processes and product quality assurance, contractors can minimize safety measures risks associated with substandard materials while maximizing customer satisfaction.
Key elements of effective Renovation Quality Control
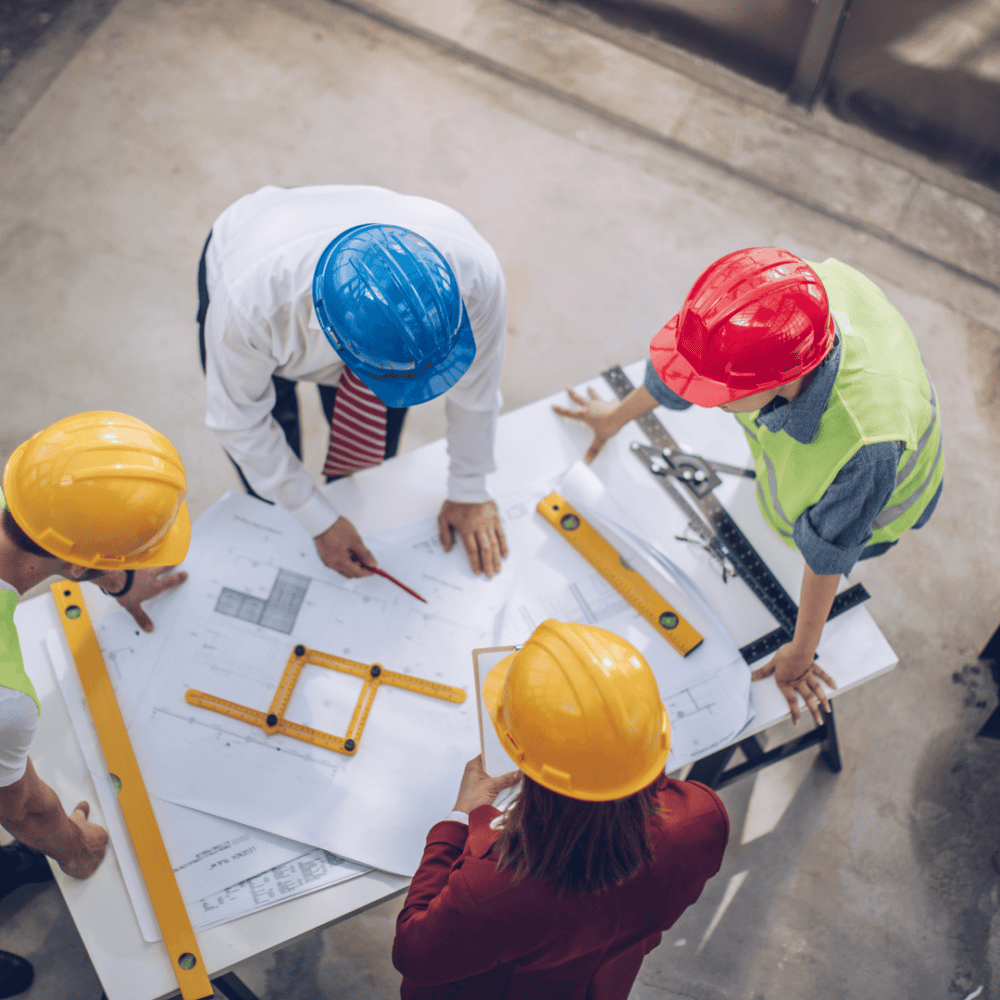
First and foremost, it is essential to have a clear and comprehensive plan in place before starting the renovation process. This plan should outline the specific goals and objectives of the project, as well as include detailed specifications and guidelines for how the work should be completed and budget constraints.
Effective communication is vital for successful renovation quality control. All parties involved in the project including contractors, subcontractors and clients should be kept informed about any changes or updates throughout the renovation process. This open line of communication allows potential issues to be identified and resolved quickly, minimizing delays and in the worst case reducing costly mistakes.
Common challenges in Renovation Quality Control
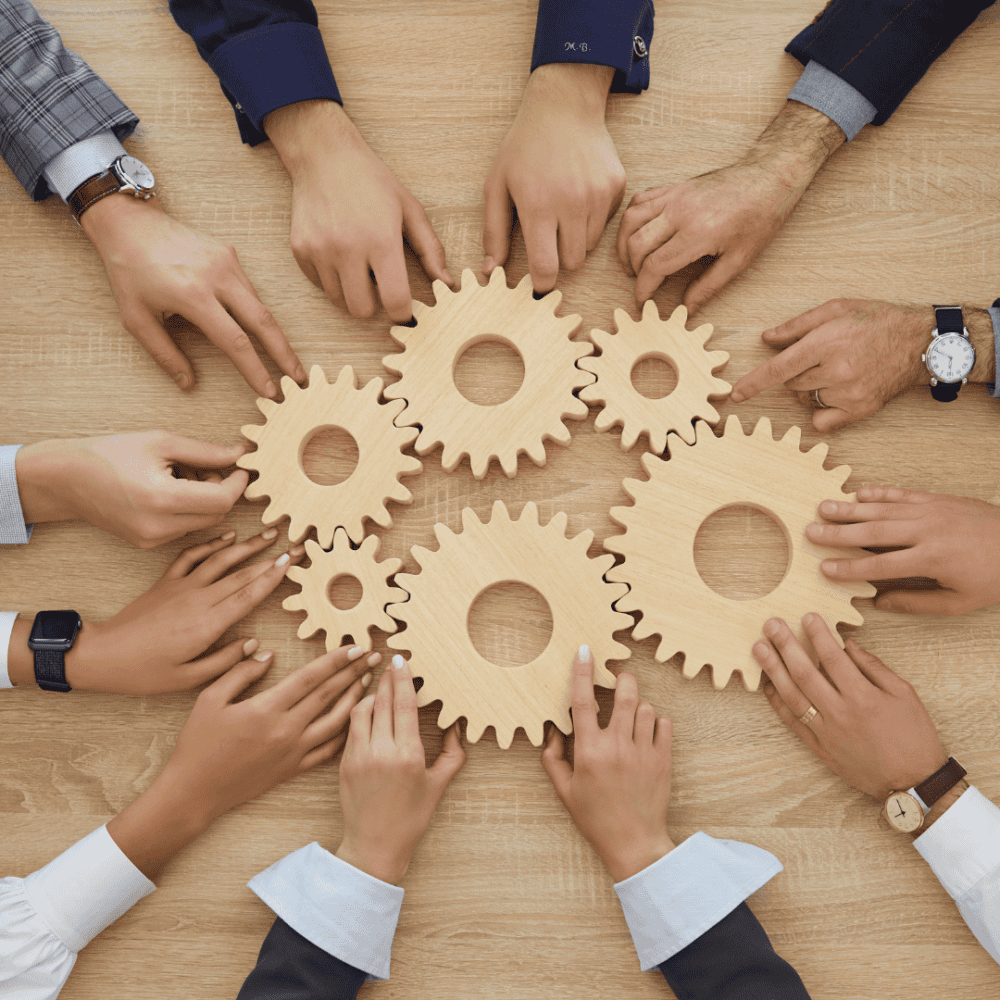
From minor repairs to major overhauls, maintaining high-quality results and standards in every aspect of the project is vital for its success. One challenge that arises frequently in renovation quality control is managing timelines effectively. With multiple tasks happening simultaneously, it’s essential to coordinate efforts and ensure that each contractor or worker completes their job on time. Delays play a crucial role and can ripple through the project, leading to increased costs and frustrated clients. By implementing strict scheduling protocols and regular type of controls and check-ins, contractors can mitigate these challenges and maintain standards over the renovation’s timeline.
Another significant hurdle in renovation quality control is achieving consistency across different phases of the project. Coordinating various tradespeople from carpenters to electricians can be tricky when they have differing opinions or work styles. Consistency ensures that there are no glaring discrepancies between areas on the project site renovated by different individuals or teams. To combat this challenge, clear communication channels must be established so that all workers are on the same page regarding expectations and desired outcomes.
Best practices for implementing Renovation Quality Control
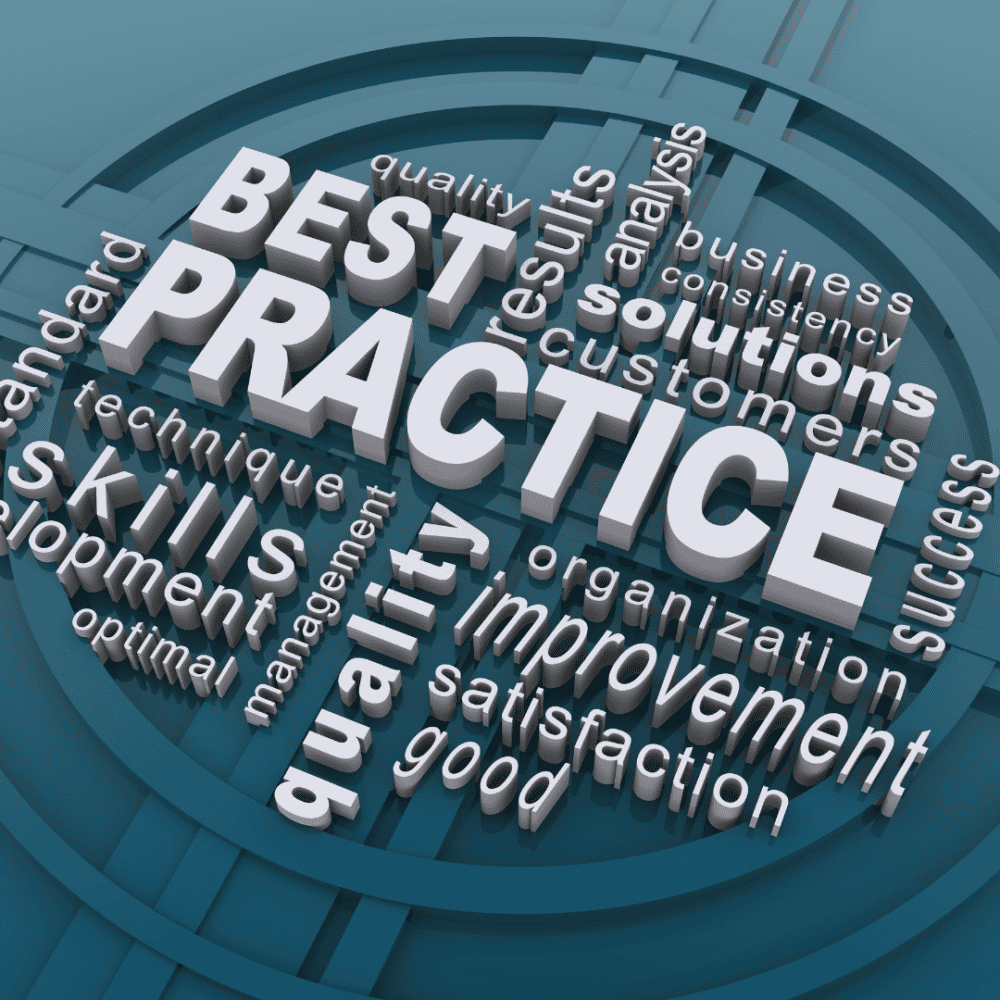
One of the best practices is to establish clear guidelines and standards before starting any renovation project. This includes defining what constitutes as acceptable quality, setting performance metrics and outlining specific procedures for evaluating workmanship and materials.
Another crucial aspect of Quality Control is regular inspections throughout the renovation process. Conducting frequent site visits allows for quick identification of potential issues or deviations from established standards. Inspections should cover all areas involved in the project, including structural components, electrical systems, plumbing fixtures, finishes and style aspects. It’s essential to involve multiple production Managers during these inspections to gain different perspectives and ensure comprehensive evaluations.
Communication plays a pivotal role in maintaining quality control during renovations. Regularly engage with contractors and construction teams to address any concerns promptly or offer guidance on specific requirements. Timely feedback can help rectify errors early on rather than waiting until completion when it may necessitate costly rework.
The benefits of a well-executed Renovation Quality Control
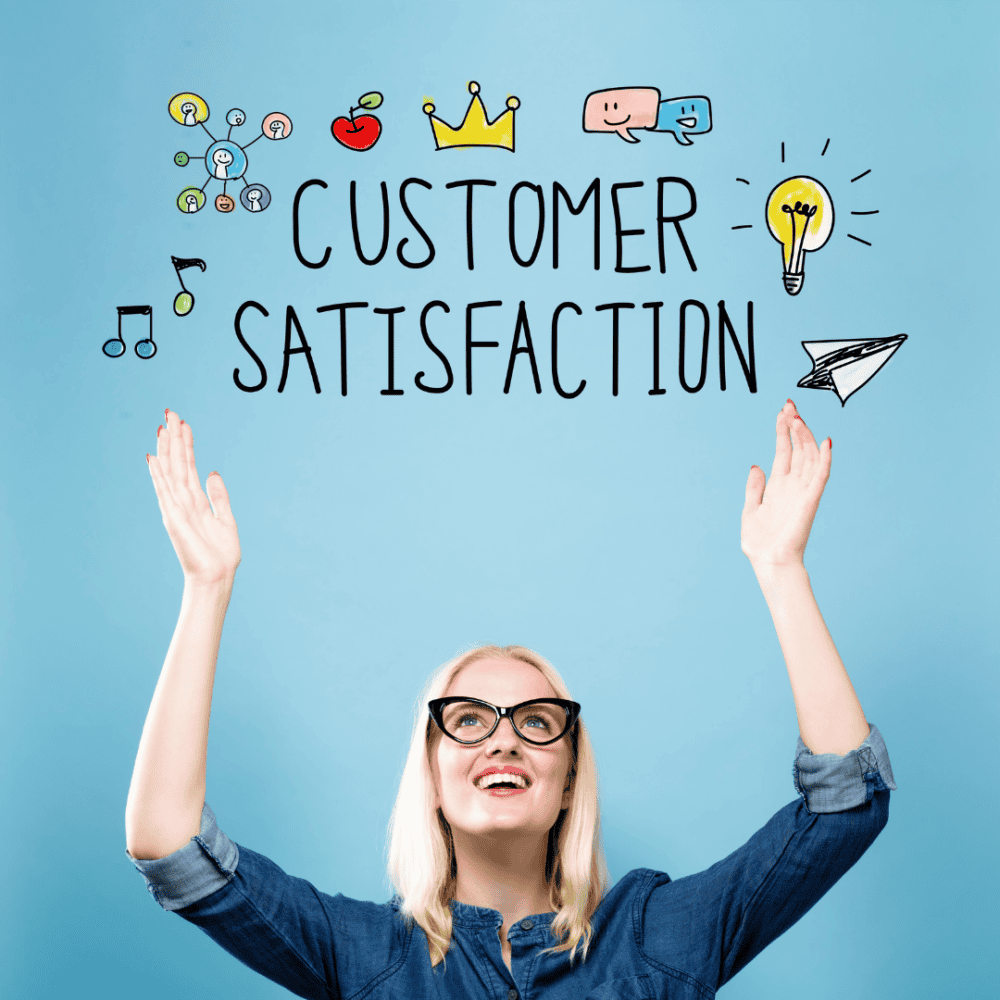
A well-executed Renovation Quality Control can have numerous benefits, making it an essential component of any renovation project quality improvement. It ensures that the work is completed to a high standard and will stand the test of time, minimizing the risk of post-renovation issues and reducing the likelihood of additional costs, repairs or rework. By implementing quality control measures from the start, such as regular inspections and performance tracking contractors can identify and rectify any potential issues in the first place early on.
Effective quality control enhances customer satisfaction by delivering a finished product that meets or exceeds their expectations. It allows homeowners to have peace of mind knowing that their investment has received the quality requirements and is being handled with care and attention to detail. Ultimately, this is a proactive approach that leads to positive reviews and word-of-mouth recommendations for contractors who prioritize quality control. Additionally, maintaining high standards throughout the renovation process also contributes to building trust between contractors and clients – an invaluable asset in creating long-term relationships within the industry and regulatory bodies.
Conclusion
Implementing a comprehensive control process during renovation projects is crucial for ensuring that the end result meets the highest standards of quality. While control measures may require an effective quality plan and additional time and resources upfront, they ultimately contribute to long-term success by reducing rework and the reactive process of enhancing reputation. It is imperative for contractors to prioritize continuous improvement and construction quality control in order to achieve excellence in every future renovation or building projects.